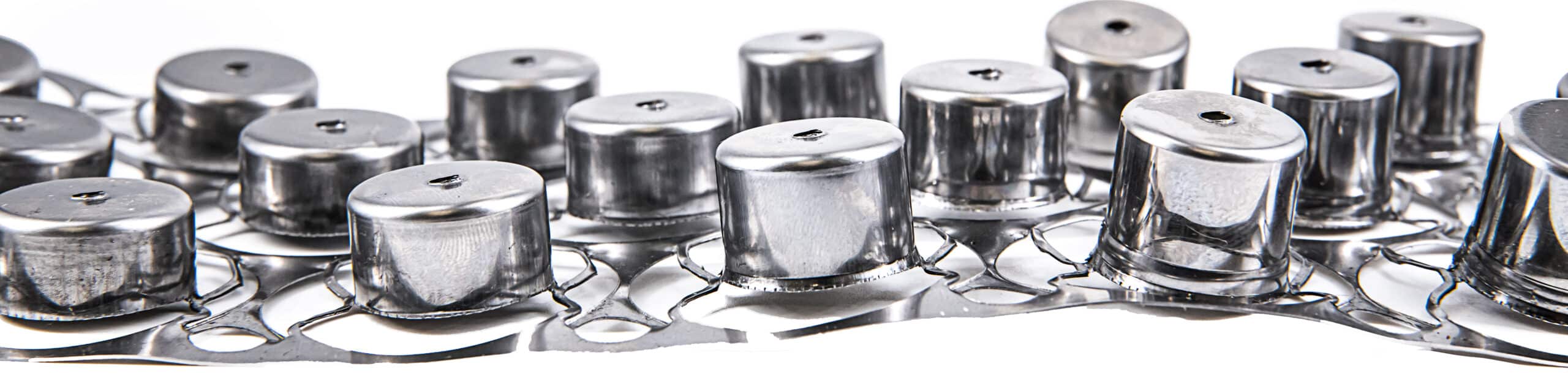
We coat parts, forming and machining tools with high-performance PVD and DLC coatings. We specialize mainly in coating components and end products for demanding applications. At the same time, we can optimize almost any common coating for better performance.
We can handle many types of coatings, below we will present the most requested ones. Do not hesitate to contact us with your specific request.
DLC Coatings
DLC (Diamond-Like Carbon) is composed of carbon with diamond-like properties, giving it exceptional strength and durability. DLC coatings provide perfect sliding contact for friction parts with high abrasion and corrosion protection.
Benefits:
-
High hardness of 3000 HV and excellent adhesion due to the unique metallic adhesion layer.
-
Attractive black colour
-
Option to tune the coating for friction contact with or without lubricants
The term DLC covers a range of different PVD and PACVD coatings, which differ in hardness, coefficient of friction for different materials and in different lubricants and, most importantly, in the way they are used.
MoSC Coatings
MoSC coating is a special type of coating that combines the properties of DLC coatings with the ultra-low friction of MoS2 compounds. It is suitable for applications that require very low friction. MoSC coatings are often used in applications where long term performance is required, such as aerospace, automotive and engineering.
Benefits:
-
Lower coefficient of friction (0.05). MoSC typically has a lower coefficient of friction than many standard coatings, improving the performance and efficiency of moving parts.
-
High thermal and chemical stability. This coating provides excellent stability in a variety of thermal and chemical environments, which is important for applications in harsh industrial environments.
StrongChrome
We apply a chrome coating to the parts to protect against corrosion and abrasion. Coating by magnetron sputtering is not harmful to the environment or people. After sputtering, the parts do not need to be ground and are coated at temperatures below 180°C.
Benefits:
-
Maintains the advantages of hard chrome without the disadvantages
-
Precise dimensions of the coating on the surface of the part
-
No need for finish grinding. After coating, the part is ready for use
AlCrN Coating
AlCrN (Aluminum-Chrome-Nitride) coating is an advanced surface material that is characterized by high hardness, wear resistance and high thermal stability. It is widely used in tooling and cutting tools, where its properties help to extend tool life and improve tool performance under high temperatures and harsh conditions. AlCrN coatings offer excellent corrosion and oxidation resistance, which is crucial for applications in harsh industrial environments. The coating is developed for high-speed dry machining of hard materials. It is used for casting aluminium, magnesium and glass.
Benefits:
-
Multiply higher tool life at dry machining and high speeds (approx. 200 m/min) than conventional AlTiN coatings
-
High oxidation resistance and can be used up to 1 100°C
-
The coating can be applied to any metallic material and other metallic finishes
-
Mirror shiny surface due to pulsed magnetron coating technology