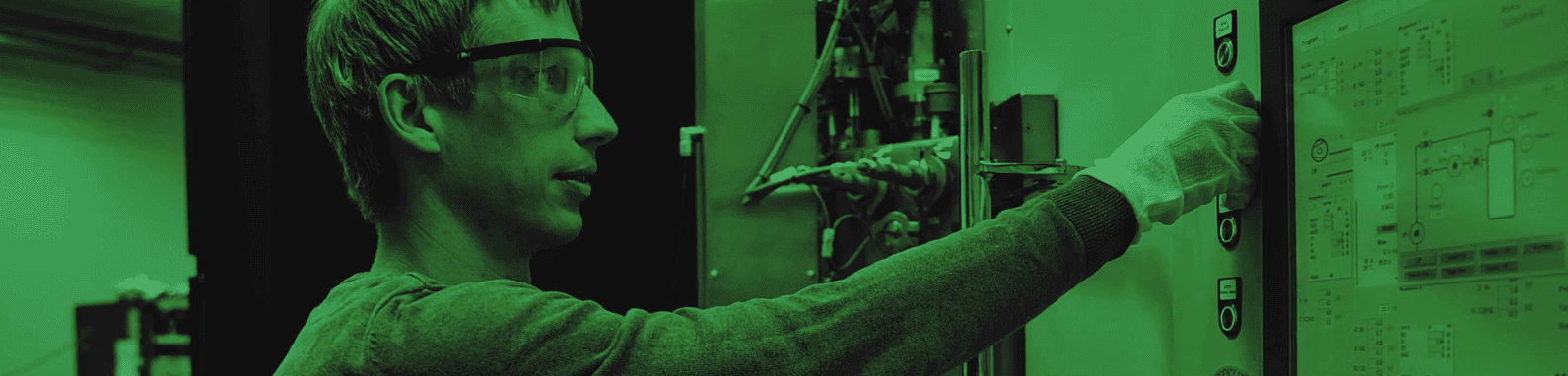
FAQ
Welcome to the Frequently Asked Questions (FAQ) page of Advamat. We are a leading supplier of advanced materials nanotechnology, providing innovative solutions for a wide range of industries. On this page you will find answers to the most frequently asked questions about coatings. If you do not find the answer to your question here, please do not hesitate to contact us. Our goal is to provide the best possible support to our customers and partners.
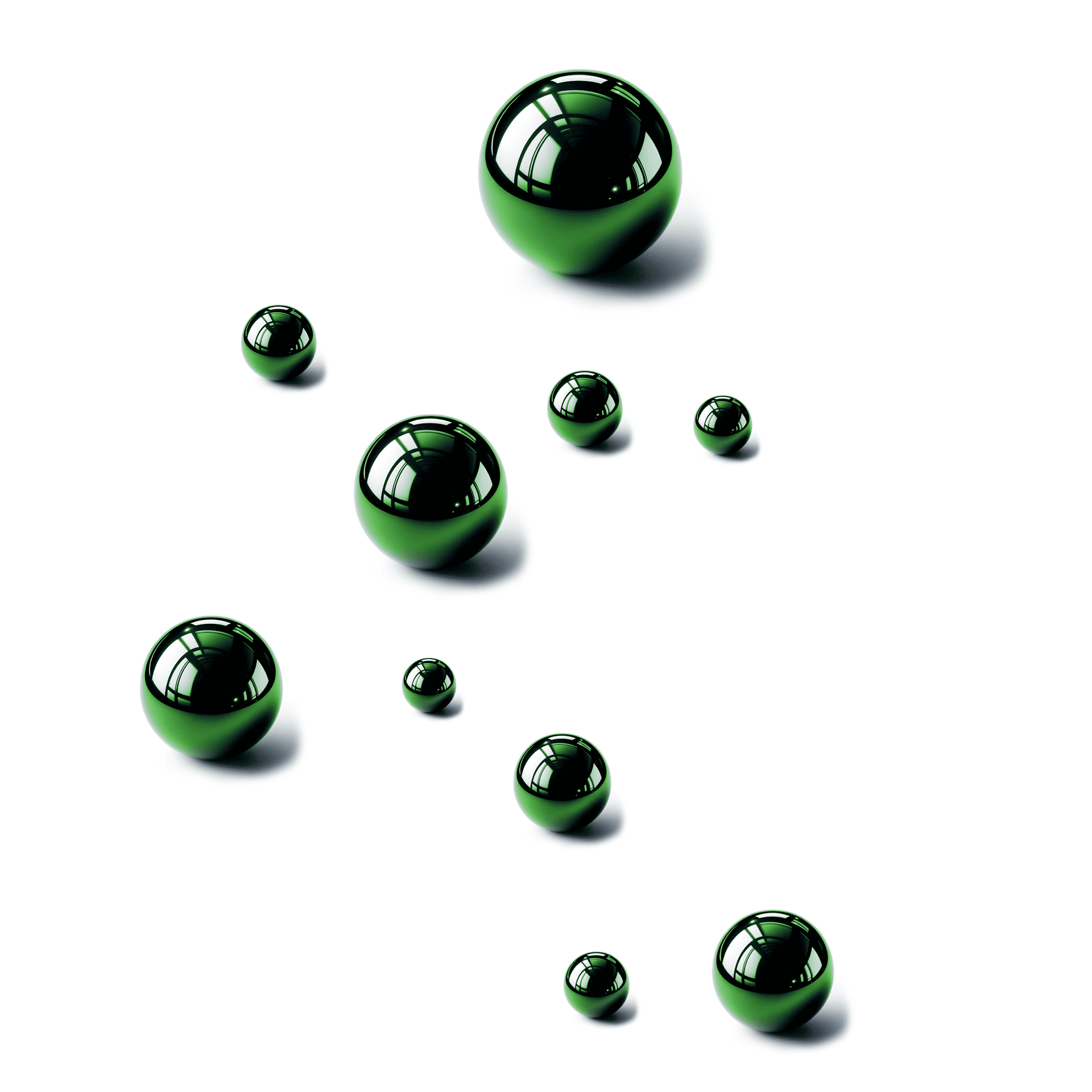